Optimism Increases with Smarter Manufacturing
Optimism Increases with Smarter Manufacturing
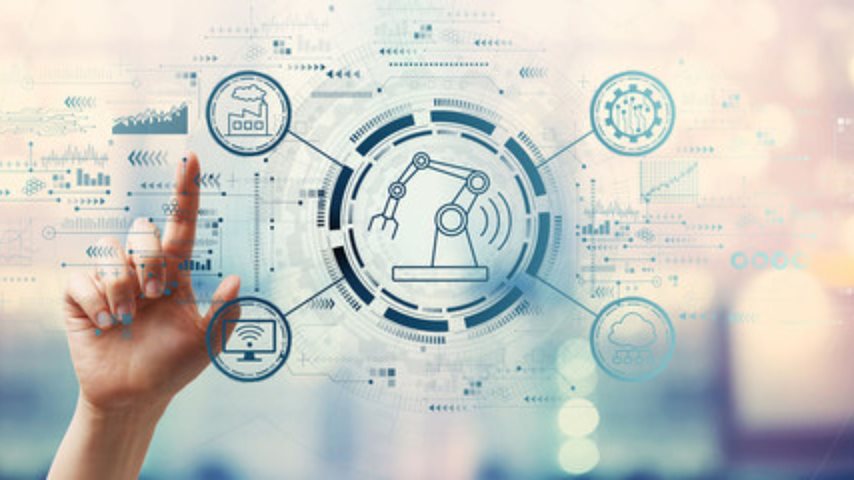
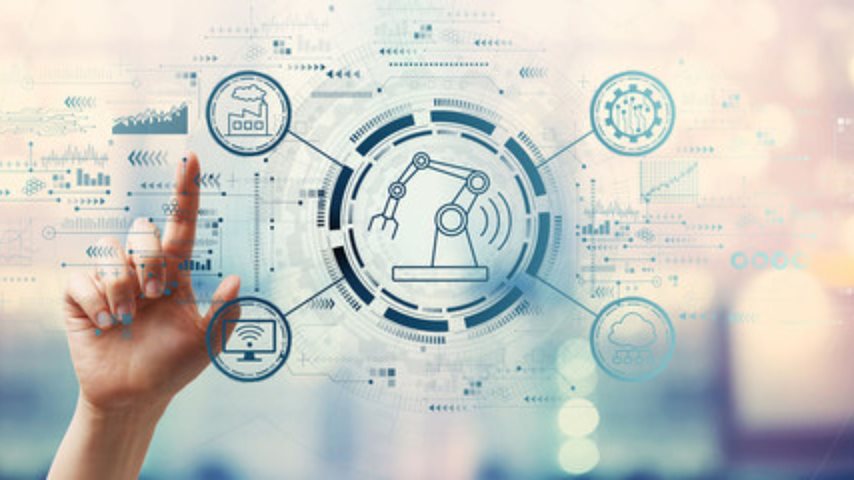
Engineers closest to digital manufacturing and smart factories report they are optimistic as organizations look ahead to Industry 4.0 and digital transformation.
Manufacturing contributes about 15.2 percent of global gross domestic product, making the segment an important part of the world economy. Examining the sector today and in the future, the value added in the manufacturing market represents over $14 trillion in 2025 and is projected to increase at a compound annual growth rate of 1.46 percent through 2029.
Earlier this year Revalize—provided a unique insight on what producers are prioritizing, their challenges, and the future of manufacturing. The company whose offerings allows manufacturers to design, model, develop, and sell their products, surveyed 500 CPQ, PLM, and engineering modeling or simulation professionals in the United States and Germany.
“Optimism is evident,” summed up Michael Umbach, chief product officer at Revalize. This confidence is not only suggested by plans by companies to increase headcount but also other key metrics.
“Ninety one percent of organizations plan to adopt new technologies, tools, or software in the next 12 months,” he explained. And when you compare their budgets for this year to last year, “70 percent have increased their budget for software.” This indicates a strong commitment to growth and innovation, which is essential to stay competitive in the rapidly evolving manufacturing landscape, he said.
“Smart Manufacturing 2025: Trends Shaping the Digital-First Era and Beyond,” reported that 57 percent of those they surveyed indicated that their organizations had increased the headcount of their teams over the last 12 months. Further, 36 percent said they were adopting new technologies, 29 percent reported that they were developing new products, and 26 percent were working to improve data security and data protection.
According to Umbach, both sustainability and artificial intelligence (AI) are crucial to manufacturing now and in the future. He pointed out that the current administration has placed “significant emphasis on AI as a cornerstone for America’s economic and national security.”
The American AI Initiative, established in February 2019 by a President Donald J. Trump Executive Order, signaled “a shift toward deregulation, promoting AI innovation, and reducing oversight and risk mitigation,” Umbach explained.
Industry 4.0 is set to “revolutionize manufacturing and the broader global economy by combining the powers of advanced technologies such as AI, the Internet of Things (IoT), big data, robotics, and automation into production processes,” the Revalize survey concluded. This is realized as “smart factories where machines communicate and optimize processes autonomously, leading to improved efficiency, less waste, and more customization.”
Worldwide manufacturing is expected to enhance the supply chain, drive employers to hire those who provide tech-driven solutions, and finally “generate a more connected, sustainable, and innovation-driven future,” the report summarized. AI will lead the change with 28 percent of those surveyed believing it to have the greatest impact on how manufacturers and engineers approach business over the next 25 years. In fact, 91 percent of those surveyed agreed their organizations are prepared to adopt and leverage Industry 4.0 technologies with 24 percent seeing these technologies having major impacts on their industries by 2050.
In fact, when thinking about the future of manufacturing, the trends and technologies that surveyed professionals will have the biggest impact included expansion of automation and robotics on the production floor (23 percent), enhanced sustainability and green manufacturing (21 percent), and implementation of IoT for real-time monitoring (21 percent).
Driven by advances in cloud computing, AR/VR, 3D printing, and digital twin technology, software that helps with simulation and modeling is moving digital technologies well beyond predictive maintenance and its sensors. The companies surveyed are using modeling and simulation in a variety of ways including performance testing (44 percent), manufacturing process simulation (37 percent), product customization (36 percent), and design verification (35 percent).
Companies are also putting their money in innovation by investing more in simulation and modeling. Almost half (47 percent) of organizations are spending more on this technology today than 12 months ago. Despite a variety of use cases and increased investment, businesses have faced challenges when implementing or adopting simulation initiatives. Top challenges include integrating technology into workflows and training team members.
Compared to German organizations, companies in the United States are more likely to use modeling and simulation for performance testing (52 percent compared to 37 percent) and design verification (40 percent compared to 31 percent). Meanwhile, technology is predicted to continue to change what modeling and simulation may look like in the future. Engineering and manufacturing professionals expect real-time simulations (45 percent) and cloud computing (42 percent) to have major impacts on their industry by 2050.
Amid this technology revolution, “engineers in manufacturing can expect a significant focus on upskilling and continuous learning,” Umbach explained. “As organizations prioritize data analysis skills, cybersecurity best practices, and knowledge of automation and control systems, it’s imperative professionals stay abreast of changes.”
Professionals report they are responding and preparing themselves and their teams for the future of manufacturing. The survey reported leaders are not only upskilling existing talent (39 percent), encouraging continuous learning (37 percent), but also staying up to date on technology trends (36 percent).
Specific tools that businesses are investing in include AI-powered quality control, Industrial IoT (IIoT) platforms, sustainable technologies, and cloud-based manufacturing. And larger organizations of 1,500 or more employees are more likely to say they will be adopting sustainable technologies (36 percent) than smaller companies.
The top five new technologies and tools that organizations were planning to adopt included AI-powered quality control (43 percent), IIoT platforms (29 percent), sustainable technologies (29 percent), cloud-based manufacturing (29 percent), and 3D printing/additive manufacturing (24 percent).
Cathy Cecere is membership content program manager.
Earlier this year Revalize—provided a unique insight on what producers are prioritizing, their challenges, and the future of manufacturing. The company whose offerings allows manufacturers to design, model, develop, and sell their products, surveyed 500 CPQ, PLM, and engineering modeling or simulation professionals in the United States and Germany.
Manufacturer optimism
“Optimism is evident,” summed up Michael Umbach, chief product officer at Revalize. This confidence is not only suggested by plans by companies to increase headcount but also other key metrics. “Ninety one percent of organizations plan to adopt new technologies, tools, or software in the next 12 months,” he explained. And when you compare their budgets for this year to last year, “70 percent have increased their budget for software.” This indicates a strong commitment to growth and innovation, which is essential to stay competitive in the rapidly evolving manufacturing landscape, he said.
“Smart Manufacturing 2025: Trends Shaping the Digital-First Era and Beyond,” reported that 57 percent of those they surveyed indicated that their organizations had increased the headcount of their teams over the last 12 months. Further, 36 percent said they were adopting new technologies, 29 percent reported that they were developing new products, and 26 percent were working to improve data security and data protection.
Industry 4.0 prioritized
According to Umbach, both sustainability and artificial intelligence (AI) are crucial to manufacturing now and in the future. He pointed out that the current administration has placed “significant emphasis on AI as a cornerstone for America’s economic and national security.” The American AI Initiative, established in February 2019 by a President Donald J. Trump Executive Order, signaled “a shift toward deregulation, promoting AI innovation, and reducing oversight and risk mitigation,” Umbach explained.

June Career Focus
This month in Mechanical Engineering: Strategies to Give Your Degree a Boost
Worldwide manufacturing is expected to enhance the supply chain, drive employers to hire those who provide tech-driven solutions, and finally “generate a more connected, sustainable, and innovation-driven future,” the report summarized. AI will lead the change with 28 percent of those surveyed believing it to have the greatest impact on how manufacturers and engineers approach business over the next 25 years. In fact, 91 percent of those surveyed agreed their organizations are prepared to adopt and leverage Industry 4.0 technologies with 24 percent seeing these technologies having major impacts on their industries by 2050.
In fact, when thinking about the future of manufacturing, the trends and technologies that surveyed professionals will have the biggest impact included expansion of automation and robotics on the production floor (23 percent), enhanced sustainability and green manufacturing (21 percent), and implementation of IoT for real-time monitoring (21 percent).
Modeling and simulation
Driven by advances in cloud computing, AR/VR, 3D printing, and digital twin technology, software that helps with simulation and modeling is moving digital technologies well beyond predictive maintenance and its sensors. The companies surveyed are using modeling and simulation in a variety of ways including performance testing (44 percent), manufacturing process simulation (37 percent), product customization (36 percent), and design verification (35 percent).Companies are also putting their money in innovation by investing more in simulation and modeling. Almost half (47 percent) of organizations are spending more on this technology today than 12 months ago. Despite a variety of use cases and increased investment, businesses have faced challenges when implementing or adopting simulation initiatives. Top challenges include integrating technology into workflows and training team members.
Compared to German organizations, companies in the United States are more likely to use modeling and simulation for performance testing (52 percent compared to 37 percent) and design verification (40 percent compared to 31 percent). Meanwhile, technology is predicted to continue to change what modeling and simulation may look like in the future. Engineering and manufacturing professionals expect real-time simulations (45 percent) and cloud computing (42 percent) to have major impacts on their industry by 2050.
Toward Industry 5.0
Amid this technology revolution, “engineers in manufacturing can expect a significant focus on upskilling and continuous learning,” Umbach explained. “As organizations prioritize data analysis skills, cybersecurity best practices, and knowledge of automation and control systems, it’s imperative professionals stay abreast of changes.”Professionals report they are responding and preparing themselves and their teams for the future of manufacturing. The survey reported leaders are not only upskilling existing talent (39 percent), encouraging continuous learning (37 percent), but also staying up to date on technology trends (36 percent).
Specific tools that businesses are investing in include AI-powered quality control, Industrial IoT (IIoT) platforms, sustainable technologies, and cloud-based manufacturing. And larger organizations of 1,500 or more employees are more likely to say they will be adopting sustainable technologies (36 percent) than smaller companies.
The top five new technologies and tools that organizations were planning to adopt included AI-powered quality control (43 percent), IIoT platforms (29 percent), sustainable technologies (29 percent), cloud-based manufacturing (29 percent), and 3D printing/additive manufacturing (24 percent).
Cathy Cecere is membership content program manager.
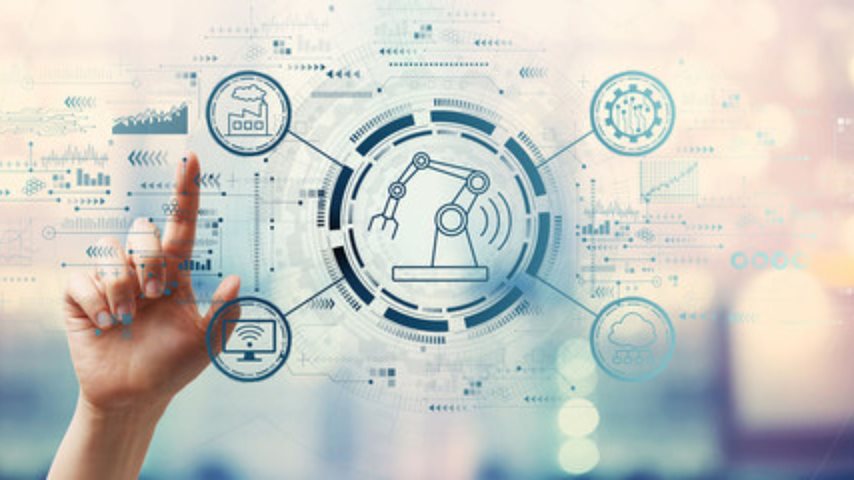
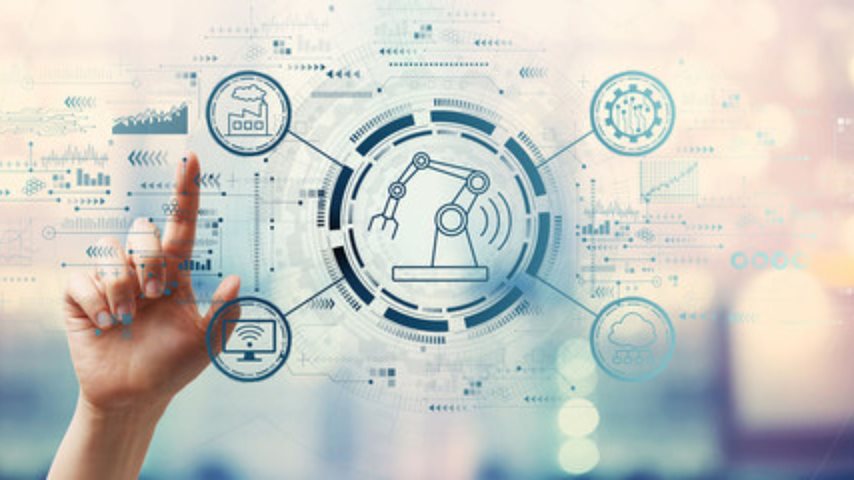