Conductive Asphalt Deices Itself
Conductive Asphalt Deices Itself
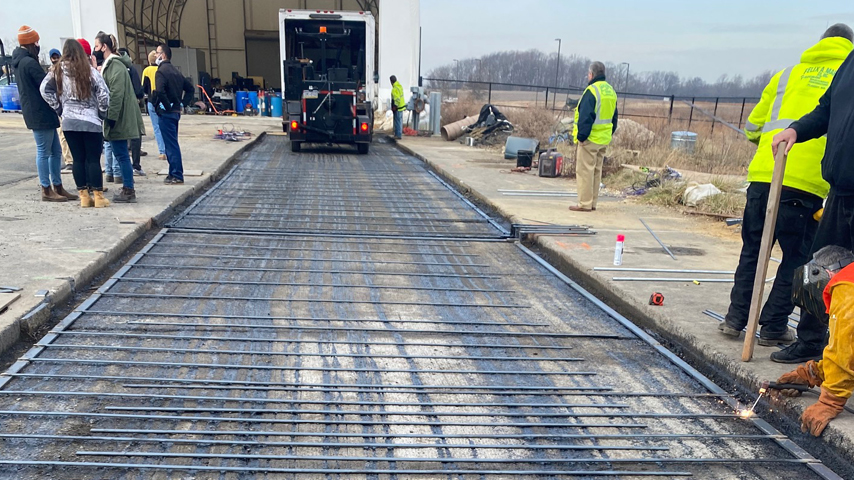
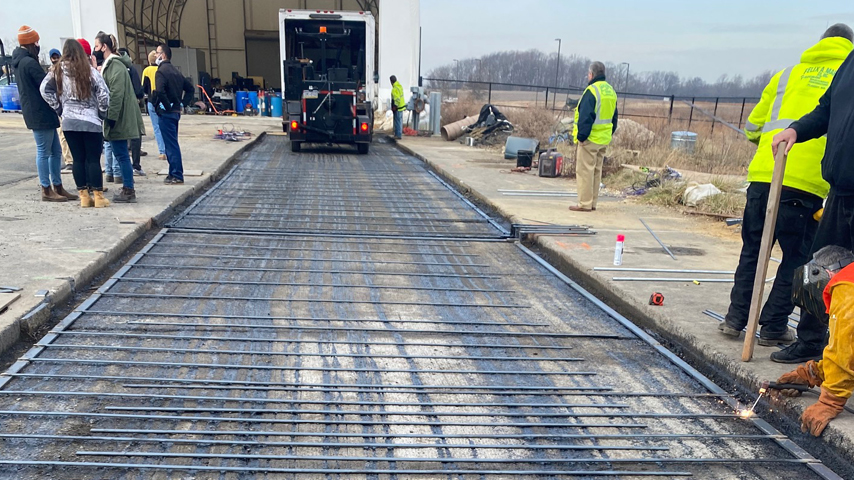
A special asphalt mix, in combination with electrodes and sensors, offers a new way to deice runways.
Safely clearing snow and ice from remote airfields can be challenging, especially with limited staff and resources. But a team at Rowan University’s Center for Research & Education in Advanced Transportation Engineering Systems (CREATES) in Glassboro, N.J., has developed a specially formulated, highly conductive upper asphalt layer that could offer a solution.
Embedded within the conductive asphalt layer is a series of electrodes and sensors, which heat the pavement surface to melt snow and ice. This work is being done in collaboration with the U.S. Department of Defense’s Cold Regions Research and Engineering Lab (CRREL) and the Engineering Research and Development Center (ERDC).
Asphalt pavement is comprised of layers of compacted sand or gravel, topped by asphalt. Site and climate factor into the thickness of each layer, as temperature changes, water intrusion, and heavy vehicle stress cause damage, resulting in an uneven surface. Improper snowplow heights may exacerbate that damage, strip sealant, and accelerate deterioration. Meanwhile, deicing salts can worsen the freeze-thaw cycle, thereby shortening an asphalt surface’s lifespan. Eliminating the use of deicing salt and snowplows through the use of conductive asphalt and embedded electrodes could mitigate many of these challenges.
Since asphalt traditionally lacks any kind of electrical conductivity and transfers energy poorly, the research team incorporated conductive materials into a standard asphalt mixture.
“We started by adding graphite and carbon fiber and then optimized the dosage to meet specifications for asphalt mixtures—in addition to making it conductive,” explained Ayman Ali, associate director of CREATES. “We were able to reduce the electrical resistivity of asphalt mixtures to between 1 to 2 Ohm.”
Become a Member: How to Join ASME
The conductive asphalt mix is comprised of 30 percent graphite and 1 percent carbon fiber by volume of asphalt binder used in the mixture.
Next, the CREATES team evaluated the large-scale constructability of the conductive asphalt mix and simulated years of regular use at Rowan University’s Accelerated Pavement Testing Facility (RUAPTF).
“We have a machine that can test the structural integrity of pavements by simulating several years of damage in a few months,” said Yusuf Mehta, a professor in Rowan University’s Department of Civil Engineering and director of CREATES. “We also looked at whether the asphalt could be manufactured to get a consistent product. We were able to do both of those successfully.”
To ensure the new asphalt would have similar performance when compared to traditional asphalt, the structural characteristics were also critical.
“When we designed this pavement, we didn't only focus on its heating performance, but also on its mechanical and structural performance and its resistance to cracking and rutting at different levels of traffic,” explained Ahmed Saidi, a post-doctoral researcher at CREATES.
Researchers conducted tests on three pavement strips to assess the conductive asphalt system’s heating and de-icing ability in cold weather applications. All three test strips were comprised of a compacted soil base layer, an existing concrete layer, and a top layer of asphalt.
Test strip 1 acted as a control, with no heating electrodes. Test strips 2 and 3 each had a layer of the conductive asphalt mixture at 0.4-inch and 1-inch thickness, respectively, in addition to a traditional asphalt layer.
Electrodes were placed perpendicular to the runway in the conductive asphalt layer at 24-inch intervals in test strip 2 and at 12-inch intervals for the first half of test strip 3 and 6-inch intervals for the latter half. In addition to the electrodes, strain gauges, pressure cells, and thermocouples were embedded in the asphalt layer of strips 2 and 3 to measure the temperatures and mechanistic responses during testing.
Improved Formula: Designing Better Concrete for SMRs
Full-scale testing in New Jersey and Alaska enabled the team to evaluate the asphalt’s performance in terms of heat conductivity and structural integrity. Multiple test cycles occurred between March 2021 and March 2022 in New Jersey, with additional testing in Alaska in fall 2023 and winter 2024.
“During testing, we embedded electrodes in the asphalt layer to transfer the electricity through the mixture and generate heat, which could potentially create weak points,” Ali said. “But based on our testing, we haven't seen any issues with it from a structural integrity standpoint. It performed similar to traditional mixtures.”
In New Jersey, test strip 3 outperformed test strips 1 and 2 with the thickest layer of conductive asphalt and closest spacing of electrodes. Test strip 2, featuring a thin layer of the conductive asphalt, consumed three times more power than test strip 3. Considering electricity rates of $0.19/kWh, the operating cost for a 1-million-square-foot area of test strip 3 amounted to $2,280 per hour.
While the operating costs of electrically heated pavement may not completely offset manual snow and ice clearing expenses, considerations for safety, continuous access, and pavement lifespan play pivotal roles in determining the suitability of pavement heating for a particular application.
“It's primarily for a shorter section of roadways like airfields and bridges, where safety and continuous operations are a major concern—they have to be a higher priority than the cost itself,” Mehta clarified.
Nicole Imeson is a writer in Calgary, Alberta.
Embedded within the conductive asphalt layer is a series of electrodes and sensors, which heat the pavement surface to melt snow and ice. This work is being done in collaboration with the U.S. Department of Defense’s Cold Regions Research and Engineering Lab (CRREL) and the Engineering Research and Development Center (ERDC).
Conductive asphalt
Asphalt pavement is comprised of layers of compacted sand or gravel, topped by asphalt. Site and climate factor into the thickness of each layer, as temperature changes, water intrusion, and heavy vehicle stress cause damage, resulting in an uneven surface. Improper snowplow heights may exacerbate that damage, strip sealant, and accelerate deterioration. Meanwhile, deicing salts can worsen the freeze-thaw cycle, thereby shortening an asphalt surface’s lifespan. Eliminating the use of deicing salt and snowplows through the use of conductive asphalt and embedded electrodes could mitigate many of these challenges.
Since asphalt traditionally lacks any kind of electrical conductivity and transfers energy poorly, the research team incorporated conductive materials into a standard asphalt mixture.
“We started by adding graphite and carbon fiber and then optimized the dosage to meet specifications for asphalt mixtures—in addition to making it conductive,” explained Ayman Ali, associate director of CREATES. “We were able to reduce the electrical resistivity of asphalt mixtures to between 1 to 2 Ohm.”
Become a Member: How to Join ASME
The conductive asphalt mix is comprised of 30 percent graphite and 1 percent carbon fiber by volume of asphalt binder used in the mixture.
Next, the CREATES team evaluated the large-scale constructability of the conductive asphalt mix and simulated years of regular use at Rowan University’s Accelerated Pavement Testing Facility (RUAPTF).
“We have a machine that can test the structural integrity of pavements by simulating several years of damage in a few months,” said Yusuf Mehta, a professor in Rowan University’s Department of Civil Engineering and director of CREATES. “We also looked at whether the asphalt could be manufactured to get a consistent product. We were able to do both of those successfully.”
To ensure the new asphalt would have similar performance when compared to traditional asphalt, the structural characteristics were also critical.
“When we designed this pavement, we didn't only focus on its heating performance, but also on its mechanical and structural performance and its resistance to cracking and rutting at different levels of traffic,” explained Ahmed Saidi, a post-doctoral researcher at CREATES.
Cold climate testing
Researchers conducted tests on three pavement strips to assess the conductive asphalt system’s heating and de-icing ability in cold weather applications. All three test strips were comprised of a compacted soil base layer, an existing concrete layer, and a top layer of asphalt.
Test strip 1 acted as a control, with no heating electrodes. Test strips 2 and 3 each had a layer of the conductive asphalt mixture at 0.4-inch and 1-inch thickness, respectively, in addition to a traditional asphalt layer.
Electrodes were placed perpendicular to the runway in the conductive asphalt layer at 24-inch intervals in test strip 2 and at 12-inch intervals for the first half of test strip 3 and 6-inch intervals for the latter half. In addition to the electrodes, strain gauges, pressure cells, and thermocouples were embedded in the asphalt layer of strips 2 and 3 to measure the temperatures and mechanistic responses during testing.
Improved Formula: Designing Better Concrete for SMRs
Full-scale testing in New Jersey and Alaska enabled the team to evaluate the asphalt’s performance in terms of heat conductivity and structural integrity. Multiple test cycles occurred between March 2021 and March 2022 in New Jersey, with additional testing in Alaska in fall 2023 and winter 2024.
“During testing, we embedded electrodes in the asphalt layer to transfer the electricity through the mixture and generate heat, which could potentially create weak points,” Ali said. “But based on our testing, we haven't seen any issues with it from a structural integrity standpoint. It performed similar to traditional mixtures.”
In New Jersey, test strip 3 outperformed test strips 1 and 2 with the thickest layer of conductive asphalt and closest spacing of electrodes. Test strip 2, featuring a thin layer of the conductive asphalt, consumed three times more power than test strip 3. Considering electricity rates of $0.19/kWh, the operating cost for a 1-million-square-foot area of test strip 3 amounted to $2,280 per hour.
While the operating costs of electrically heated pavement may not completely offset manual snow and ice clearing expenses, considerations for safety, continuous access, and pavement lifespan play pivotal roles in determining the suitability of pavement heating for a particular application.
“It's primarily for a shorter section of roadways like airfields and bridges, where safety and continuous operations are a major concern—they have to be a higher priority than the cost itself,” Mehta clarified.
Nicole Imeson is a writer in Calgary, Alberta.