3D-Printed Bicycle Headed for Olympics
3D-Printed Bicycle Headed for Olympics
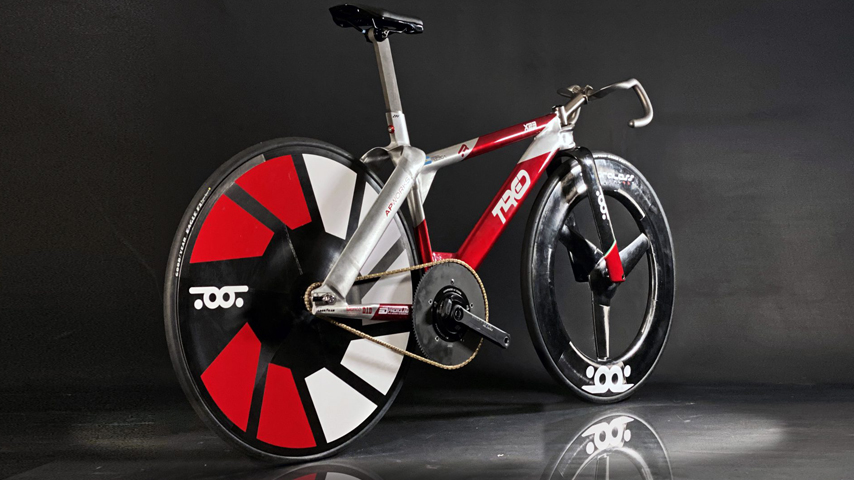
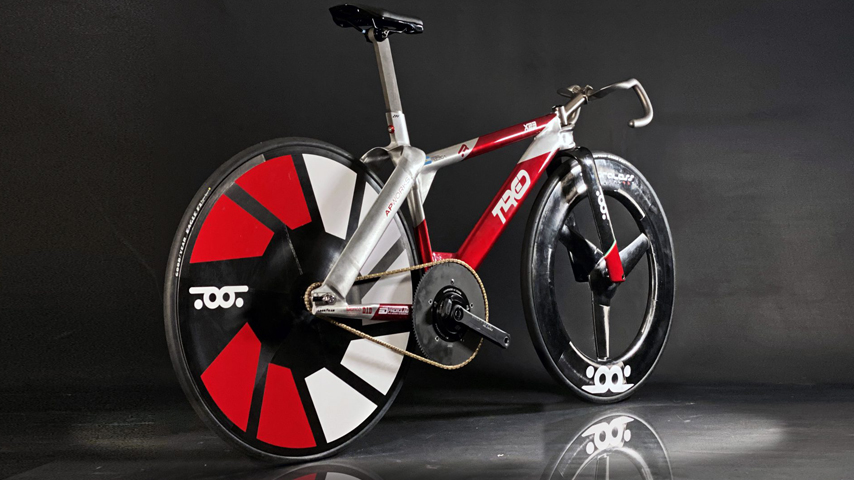
A bespoke track bike made from a high-tech alloy will compete in Paris this summer.
Most vehicles designed and engineered for speed have extremely aerodynamic shapes to minimize air resistance. There’s a limit to how much streamlining can be done with racing bicycles, however, as each one has a not-very-aerodynamic rider sitting on top. Not only do these non-rigid forms catch air, but each one is different.
Racing bikes can be tailored for the individual athlete, but doing so is a long and expensive affair.
Unless you use 3D printing.
That’s just what the makers of Toot Engineering’s X23 track bike have been up to. By turning to additive technology, they have been able to go through multiple iterations to meet the specific needs of specific riders. The resulting bike has an architecture that wouldn’t be possible otherwise.
Thanks to their successes, the X23 is slated to be raced by the Argentinian team in the 2024 Olympics in Paris.
More on Additive Manufacturing: Students 3D Print Heat Shield
“From a mechanical engineering point of view, it’s an area where you design something, you produce something, and the day after it’s in the field. There is no industry where the loop is so close—it’s incredible,” said Ferdinando Auricchio, a professor of solids and structural mechanics at the University of Pavia and one of the engineers who helped build the X23. “The bicycle is a funny area, because if you look at the bicycle, you look at something that seems extremely simple—and mechanically it is simple. But it’s also a really high-end application. You need to be at the border of performance and technology.”
The parts of the X23 are printed separately, out of a variety of materials, and then welded and assembled. The frame is made of Scalmalloy, an alloy of scandium, aluminum, and magnesium. Other parts are titanium or steel. The bike would be lighter, to be sure, if it were made of carbon fiber, but the extra weight won’t mean much on the hill-free Olympic track.
“You can, for example, sacrifice up a small part of the weight, but then you can enhance the stiffness, which is more important in this kind of race,” said Gianluca Alaimo, a mechanical engineer at the University of Berea, who also worked on the bike.
The extra weight is more than made up for by the ability to print cheaply and repeatedly, fine-tuning the shape by millimeters, and measuring vibrations and deformations with each round.
“We can print quickly with steel,” Auricchio said. “And we’ve proven that with steel we’re getting much better behavior than other more advanced material. If you give me a machine with a better material, I can do even better.”
The funky super-narrow steel handlebars, for instance, are an architecture not easily made with other technologies. After repeated iterations, the Toot team was able to reduce the weight by 25 percent while keeping the same stiffness. More importantly, the handlebars are made to fit the posture, grip, and weight of the racer who will be using them.
To do that, a first prototype is done in plastic, meant only for the bicyclist to try out and offer feedback. Then, once it has been produced in metal, the bike and rider are put in a wind tunnel, and the resultant data is used to further tweak the design, after which it is printed out and tested all over again, a process that takes about 24 hours.
“Let’s say that he tries it out on the field, then gives us feedback. We do new simulations, we 3D print it in metal, give it to him, and then he tells us it’s OK, it’s not good, or let's do it a different way,” Auricchio said. “It’s an iterative process.”
Improve Your Skills: Design for Additive Manufacturing with Metals
Future handlebars might be altered and printed to fit the needs not only of specific racers but of specific courses—a design that might work for a track with only left turns would be different for a twisty course.
The X23 had its debut at the UCI Track World Championships in August, and now 16 parts have been approved for us in the 2024 Olympics in Paris that start in July.
“We're having fun, and we’re learning a lot,” Auricchio said. “And, you know, they are winning.”
Michael Abrams is a science and technology writer in Westfield, N.J.
Racing bikes can be tailored for the individual athlete, but doing so is a long and expensive affair.
Unless you use 3D printing.
That’s just what the makers of Toot Engineering’s X23 track bike have been up to. By turning to additive technology, they have been able to go through multiple iterations to meet the specific needs of specific riders. The resulting bike has an architecture that wouldn’t be possible otherwise.
Thanks to their successes, the X23 is slated to be raced by the Argentinian team in the 2024 Olympics in Paris.
More on Additive Manufacturing: Students 3D Print Heat Shield
“From a mechanical engineering point of view, it’s an area where you design something, you produce something, and the day after it’s in the field. There is no industry where the loop is so close—it’s incredible,” said Ferdinando Auricchio, a professor of solids and structural mechanics at the University of Pavia and one of the engineers who helped build the X23. “The bicycle is a funny area, because if you look at the bicycle, you look at something that seems extremely simple—and mechanically it is simple. But it’s also a really high-end application. You need to be at the border of performance and technology.”
The parts of the X23 are printed separately, out of a variety of materials, and then welded and assembled. The frame is made of Scalmalloy, an alloy of scandium, aluminum, and magnesium. Other parts are titanium or steel. The bike would be lighter, to be sure, if it were made of carbon fiber, but the extra weight won’t mean much on the hill-free Olympic track.
“You can, for example, sacrifice up a small part of the weight, but then you can enhance the stiffness, which is more important in this kind of race,” said Gianluca Alaimo, a mechanical engineer at the University of Berea, who also worked on the bike.
The extra weight is more than made up for by the ability to print cheaply and repeatedly, fine-tuning the shape by millimeters, and measuring vibrations and deformations with each round.
“We can print quickly with steel,” Auricchio said. “And we’ve proven that with steel we’re getting much better behavior than other more advanced material. If you give me a machine with a better material, I can do even better.”
The funky super-narrow steel handlebars, for instance, are an architecture not easily made with other technologies. After repeated iterations, the Toot team was able to reduce the weight by 25 percent while keeping the same stiffness. More importantly, the handlebars are made to fit the posture, grip, and weight of the racer who will be using them.
To do that, a first prototype is done in plastic, meant only for the bicyclist to try out and offer feedback. Then, once it has been produced in metal, the bike and rider are put in a wind tunnel, and the resultant data is used to further tweak the design, after which it is printed out and tested all over again, a process that takes about 24 hours.
“Let’s say that he tries it out on the field, then gives us feedback. We do new simulations, we 3D print it in metal, give it to him, and then he tells us it’s OK, it’s not good, or let's do it a different way,” Auricchio said. “It’s an iterative process.”
Improve Your Skills: Design for Additive Manufacturing with Metals
Future handlebars might be altered and printed to fit the needs not only of specific racers but of specific courses—a design that might work for a track with only left turns would be different for a twisty course.
The X23 had its debut at the UCI Track World Championships in August, and now 16 parts have been approved for us in the 2024 Olympics in Paris that start in July.
“We're having fun, and we’re learning a lot,” Auricchio said. “And, you know, they are winning.”
Michael Abrams is a science and technology writer in Westfield, N.J.
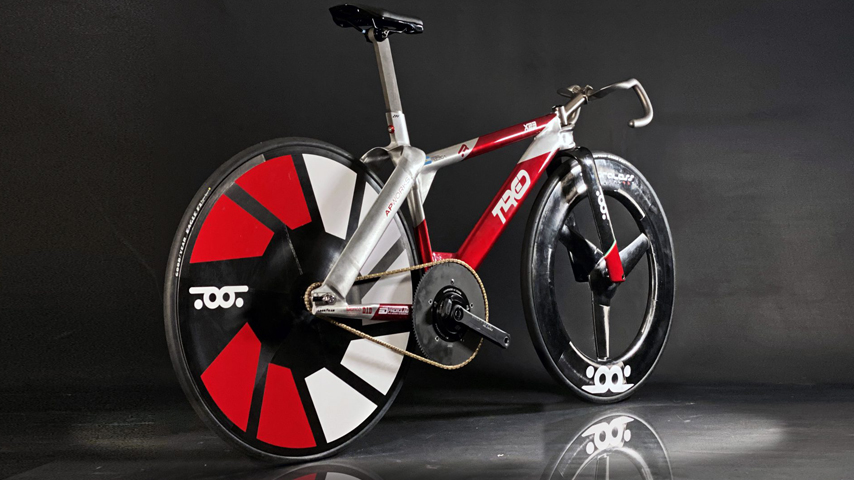
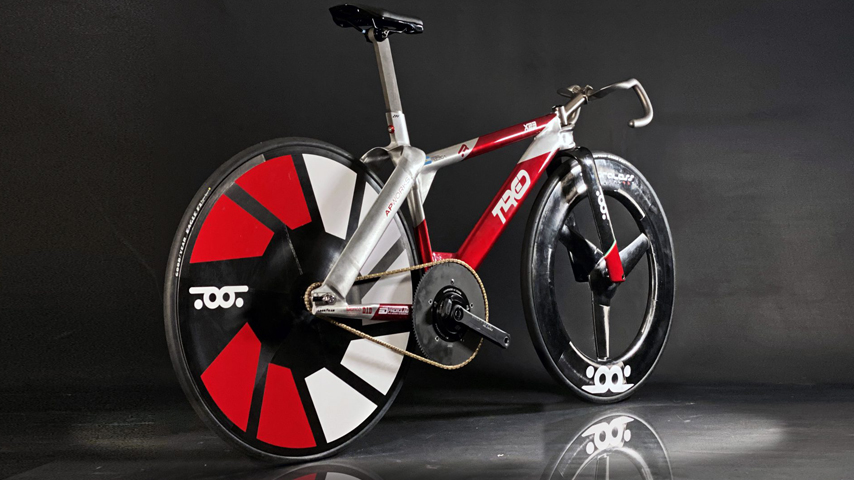