But the “future of space exploration is dependent on technologies that maximize mission endurance and self-sufficiency. As missions venture further away from Earth, resupply logistics fail to accommodate the probability of component failure and uncertainty about which component may fail,” according to “In-Space Additive Manufacturing: A Review,” published in ASME’s Journal of Manufacturing Science and Engineering in February 2023.
In-space manufacturing (ISM), of which in-space additive manufacturing (ISAM) is a part, is a promising solution, the study suggests, which would integrate repair and fabrication techniques into space missions, “providing on-demand capabilities to adapt to unforeseen situations.”
The study provides a literature review of ISAM and its related technologies and summarizes numerous studies available on this subject, while also discussing ISAM and identifying knowledge gaps.
Lead author Miguel Hoffmann, a doctoral student at the Wm Michael Barnes ‘64 Department of Industrial and Systems Engineering at Texas A & M University, and principal investigator Alaa Elwany, associate professor and ASME Foundation Swanson Fellow, College of Engineering Eugene Webb Faculty Fellow, and director of the Texas A&M Metal Additive Manufacturing Research Laboratory (AMTex), recently shared some additional insights on ISAM and what may lie ahead.
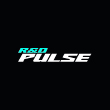
Could you tell us about the origins of this research?
Elwany
I have been working on research in additive manufacturing (AM) and smart manufacturing (SM) for the past 10 years. A big portion of my research portfolio focuses on how AM can revolutionize the aviation and aerospace sectors through creating complex parts from innovative materials with unique properties to meet performance requirements of these sectors.
Recently, I developed even more interest in the applications of AM for space exploration. In 2019, I was member of a multi-university team led by the University of California, Davis, that was awarded a project sponsored by NASA. Our NASA Space Technology University Institute (STRI) focuses on developing fundamentally disruptive approaches for the design of deep-space habitats to safely execute human-exploration missions. One important enabler to achieve this is to provide the capability of repairing parts—or producing replacement parts—at the habitat’s location. AM is an ideal set of emerging technologies that can potentially provide this capability, but significant research and development has yet to be conducted to make them suitable for micro-gravity environments. This research published in ASME is part of that project.
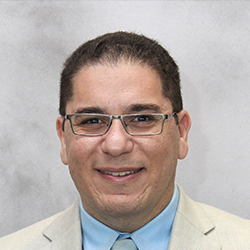
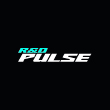
Let’s talk about the ISM operational scenarios mentioned in the report. What are the key differences among them? Why is this important?
Hoffman
The operational scenarios refer to different environments in which the manufacturing technology will be deployed, which in turn dictates constraints and available resources. Some of the key differences include gravity and pressure levels, platform-related constraints—e.g., limited footprint, power—and scale of the products to be fabricated.
For example, additive manufacturing that relies on feedstocks in powder form such as powder bed fusion and binder jetting are often regarded as incompatible with ISM, and they certainly would introduce many challenges for intravehicular ISM. However, these processes may be good candidates for planetary ISM, as they can be coupled with in-situ resource utilization. The operational scenario is, therefore, the basis of ISM.
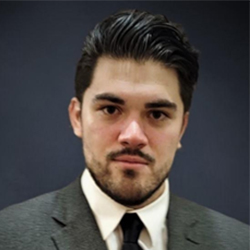
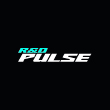
In what ways is additive manufacturing complicated by conditions in space? What are some of the vital challenges that researchers are looking to overcome?
Elwany
There are technical challenges associated with AM technologies when using them to produce parts even on earth, let alone space conditions. Those include the high susceptibility of printed parts to defects such as pores and cracks due to the complex physics involved in the manufacturing process. Now add microgravity to these challenges, and a task as simple as handling raw material or just grabbing the manufactured part from the 3D printer become tremendously complicated before starting to think about the quality of the part. The physics of the material being processed during AM involve melting, solidification, and other phenomena that are extremely difficult to control in microgravity.
One other challenge is related to the premise of habitats for deep space exploration. Those habitats will not always have humans on board. A task as simple as just extracting the printed part from the machine and then performing some simple finishing requires very careful planning to automate. Finally, many of the parts produced using AM require post-manufacturing processing that require a high power source, for example to heat the part to elevated temperatures, which is obviously a limitation if we think of the deep space habitat environment.
Researchers typically follow one of two routes: Either to improve and modify current AM processes to address the challenges noted above, or to develop new AM processes that are suitable for use in micro-gravity or are easier to automate. We focus on the latter approach in other publications that will come out of this project.
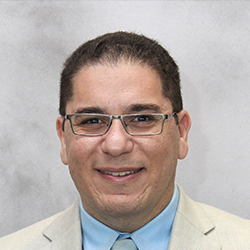
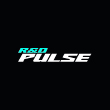
Could you discuss some of the in-space manufacturing technologies you see as the most promising and why?
Hoffman
Future ISM technologies will need to be hybrid, incorporating other capabilities in addition to additive. For example, subtractive capabilities, sometimes known as machining, are needed to finish parts with more stringent quality requirements, and inspection capabilities are needed to ensure that the produced parts meet design requirements.
Future ISM technologies will mostly differ by AM process. Directed energy deposition (DED) is ubiquitous in hybrid manufacturing and is one of the two candidate processes for ISM of metallic parts. DED can process metal wire feedstock as opposed to powders, and be incorporated into 5-axis platforms. DED can also produce large-scale architectures, for instance, by incorporating the printhead as the end effector of a robotic arm, so it could be demonstrated for either intravehicular or extravehicular ISM operational scenarios.
The other promising ISM technology employs material extrusion (MEX). Filament-based material extrusion is by far the most validated ISM process, with hundreds of polymeric parts printed aboard the International Space Station (ISS). The user-friendly system architecture and the capability of easily switching extruders enable MEX to process a wide range of materials with minimal human interaction. If suitable thermal post-processing can be implemented, MEX may also enable the ISM of metals and ceramics.
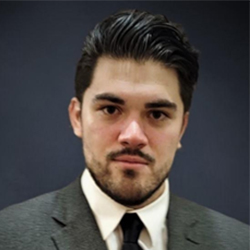
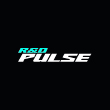
What are the prospects for in-space manufacturing moving forward? How does your team proceed with additional research in this vein? Or are there new topics you’re looking to explore?
Elwany
In-space manufacturing has advanced significantly over the past five years. It is identified as one of the R&D priorities in the 2022 White House’s National Strategic Plan on Advanced Manufacturing in the U.S., and both federal and private investments to advance in-space manufacturing capabilities continue to grow. For example, the National Institute of Standards and Technology (NIST) recently funded a project to develop a roadmap to define research needs for in-space manufacturing.
My team plans to continue research in this direction. As we finalize our new space-friendly AM process and validate it, our next step would be to optimize that manufacturing process to produce parts with superior quality suitable for space applications. Next, we will work on developing modeling and predictive capabilities that are needed to certify a printed part for deployment. We also have a very strong focus on technology transition, which will involve demonstrating our process in space conditions after its development and validation in the laboratory.
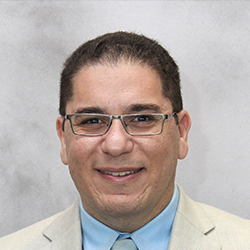
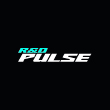
Do you have any additional thoughts you would like to share?
Elwany
When AM was “revived” in the first decade of the 2000s, many thought that it has limitations and can only be used for prototyping at best. After careful and coordination R&D, we now see 3D-printed parts used in very critical applications inside patients’ bodies as implants or aboard aircraft as engine components. Similar voices now suggest that AM technologies will not be able to overcome the barriers of micro-gravity. I expect that with advancements similar to what happened with terrestrial AM, in-space AM will be able to overcome those barriers and effectively support and advance space exploration. Outcomes from those advancements in AM technologies will also have tremendous benefits for terrestrial applications.
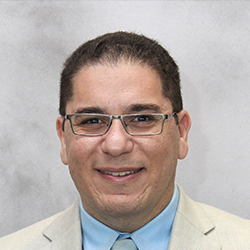