But the “future of space exploration is dependent on technologies that maximize mission endurance and self-sufficiency. As missions venture further away from Earth, resupply logistics fail to accommodate the probability of component failure and uncertainty about which component may fail,” according to “In-Space Additive Manufacturing: A Review,” published in ASME’s Journal of Manufacturing Science and Engineering in February.
n-space manufacturing (ISM), of which in-space additive manufacturing (ISAM) is a part, is a promising solution, the study suggests, which would integrate repair and fabrication techniques into space missions, “providing on-demand capabilities to adapt to unforeseen situations.”
The study provides a literature review of ISAM and its related technologies and summarizes numerous studies available on this subject, while also discussing ISAM and identifying knowledge gaps.
Lead author Miguel Hoffmann, a doctoral student at the Wm Michael Barnes ‘64 Department of Industrial and Systems Engineering at Texas A & M University, and principal investigator Alaa Elwany, associate professor and ASME Foundation Swanson Fellow, College of Engineering Eugene Webb Faculty Fellow, and director of the Texas A&M Metal Additive Manufacturing Research Laboratory (AMTex), recently shared some additional insights on ISAM and what may lie ahead.
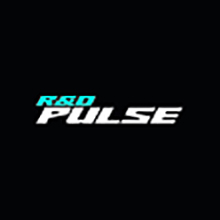
How big a problem are defective rails for the railroad industry today?
Speaker Man
It's estimated that between 1980 and 2014, American freight railroads spent $575 billion toward improving its infrastructure. That means for an industry that is all privately funded, it spent 40 percent of its overall revenue to stay ahead in terms of safety and efficiency. The Federal Railroad Administration (FRA) keeps safety records showing the impact of various internal rail flaws. According to these FRA statistics, in the past decade, for example, transverse defects in rails in the U.S. have typically caused about 100 derailments per year and about $25 million in direct damage costs per year (without including the indirect costs). So any improvement in rail flaw detection is quite relevant to the efficiency and the safety of rail transportation.
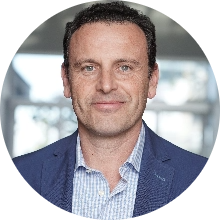
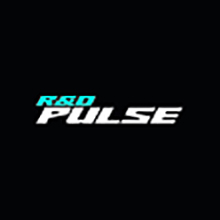
Why is ultrasonic testing the most popular nondestructive testing method used on rails today?
Ultrasonic testing has proven itself as the most accurate method to detect internal rail flaws that, if left undetected, can cause dangerous and costly derailments. The technique uses relatively inexpensive hardware and is well understood and proven in a variety of inspection applications, including rails. The typical deployment of ultrasonic testing for rail flaw detection uses fluid-filled wheels (Rolling Search Units or RSUs) hosting piezoelectric transducers that launch and detect ultrasonic waves into and from the rail at frequencies between 2 MHz and 5 MHz as they roll over the rail top surface. These RSUs are typically mounted on specialized inspection vehicles (hi-railers) that conduct the inspection at speeds up to 30 mph to 35 mph.
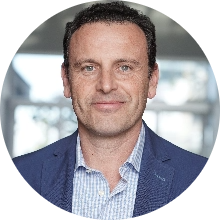
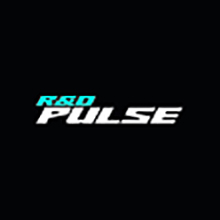
How does your system work?
Instead of rolling wheels and MHz-type waves, our approach utilizes noncontact, air-coupled transducers arranged in pairs to track the ultrasonic wave propagation between two sections of the rail at frequencies in the kilohertz range. Special signal processing developed for “passive ultrasonic testing” is used to track ultrasonic signatures without the use of the typical pulsating source, and instead relying on the natural acoustic excitations from the train wheels or a continuous excitation. Since the technique uses completely noncontact transduction and continuous (rather than pulsed) excitation, it lends itself to high-speed testing, that is, at speeds at least equal to the normal revenue speed of trains (around 60 mph). Furthermore, the use of lower frequencies ensures better penetration into the rail including cases of surface shelling that typically constitute a barrier to the high-frequency waves used in conventional RSUs.
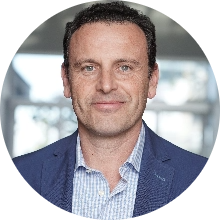
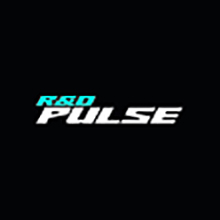
What are the challenges of current railway ultrasonic testing that your high-speed, passive, and noncontact technique seeks to overcome?
Today’s RSU units provide a very valuable inspection tool for rails. However, challenges exist to penetrate surface shelling and to increase the testing speed to more than 30 mph with these systems. The inspection vehicles used today have to be scheduled around normal train operations therefore limiting the number of tests that can be done in a given rail segment in a given time.
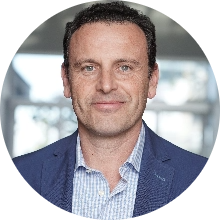
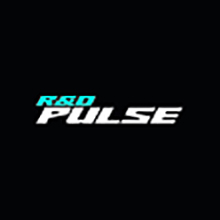
When you compare your technique with the current technology in use, what are the benefits?
The goal of our research in this area is to develop a rail inspection technology that is deployable by a train during its normal operations. In other words, we aim at making each train a “smart train,” able to detect internal rail flaws during a regular run. This mode of rail inspection would therefore be “transparent” to normal traffic, without requiring special scheduling. In addition, the ability of each train to perform rail inspection would surely improve the reliability of defect detection (while decreasing the probability of false alarms) by exploiting the test redundancy that would be afforded by the multiple train passes over the same rail. Having said this, the current state of development of the technology does not suggest a potential complete replacement of the conventional RSUs for rail inspection, but rather an additional tool in the hand of the railroad maintenance engineer. For example, our technology could enable engineers to detect the larger defects at revenue speeds, but may have challenges in detecting the smaller defects in certain locations within the rail cross-section that instead remain good targets of RSUs.
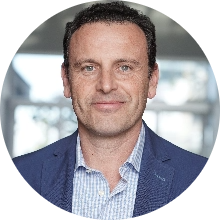
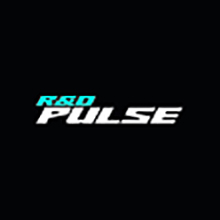
You are in the prototype stage, how feasible is commercial acceptance within the next five years?
The rate of false alarms computed in recent testing is still too high for field implementation of this technique. We're now working to reduce the rate to acceptable levels. One area of investigation is the use of a continuous acoustic source to supplement the wheel excitations and also provide better signal stability when there is low excitation such as during slow speeds. We are currently analyzing the data obtained from the most recent tests that used these improvements.
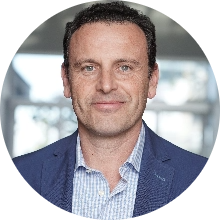